Ultra High Purity Gases for Semiconductors
We are a leading supplier of ultra high purity gases including halocarbons, hydrocarbons and other reactive gases also named as electronic specialty gases (ESGs). We support custom gases and mixtures that are required for specific applications in variety of semiconductor related industries such as fiber optics, III-V, Flat Panel displays, IC packaging, Photovoltaics, PCBs and Equipment surface treatments.
Our portfolio of ultra-high purity gases and advanced materials are aligned with tight quality controls to support semiconductor manufacturing globally. Ultra-high purity gases and advanced materials for sub 7nm technologies are used as dopants, deposition of thin films, etching of selective films, cleaning of deposition chambers, ultra-high purity rare gases and gas mixtures for lithography and other custom applications.
Emerging semiconductor processes at <7nm and beyond face extreme reliability and yield challenges. Ultra-high purity process gases and materials are required to ensure process repeatability. Novel applications using new gases and mixtures emerge not only in the front-end of the line (FEOL) such as FINFETs and GAAFET but also in the back end of the line (BEOL) in metallization. These gases are required for a variety of specific applications that address area selective etch with desired etch rates and selectivity, to manufacture semiconductor devices with transistors at tight 5nm and 2 nm geometries.
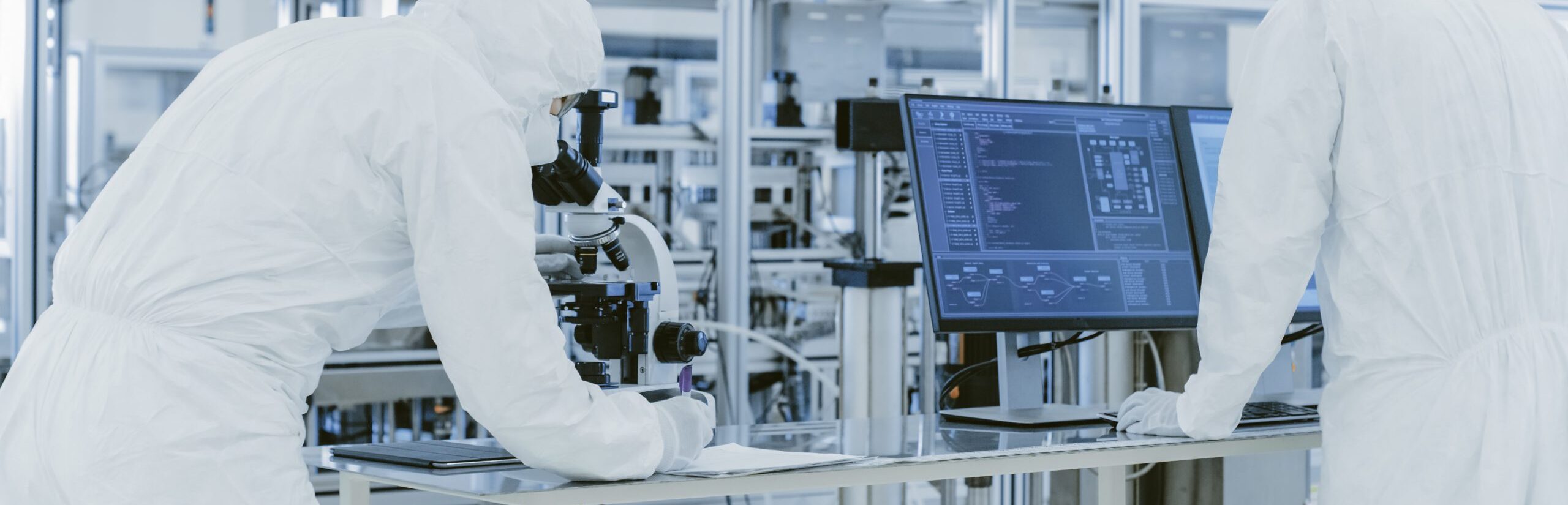
Meeting Industry Standards
Fabrication of a high-performance device structure requires a variety of gases that can be used in both deposition and etch process. Like deposition of thin film with defined electrical properties, etch gases are designed to remove specific materials, for example silicon nitride, silicon oxide, and metals. With shrinking dimensions and increasing device density etch process face new critical dimension challenges. Innovative etch molecules are needed to overcome integration and design challenges and enable production of emerging advanced nodes. EFC offers a wide variety of etch chemistries for selective and custom etch.
Hydrocarbon gases: Used in carbon doping for dielectrics films. They are also used in anti-reflecting coatings (ARC) and as hard masks (HM). For example, Methane, Ethylene, Propylene, 1-Butene and others.
Dopant gases: Boron, Phosphorous and Arsenic are dopants in Silicon for PMOS and NMOS in CMOS devices. For example, Diborane, Arsine, Phosphine are frequently used.
Deposition gases: Used in deposition of epi-Silicon and polysilicon. For example, Disilane, Dichlorosilane along with others.
Dielectric etch gases: A variety of gases with varying fluorine content are used for etching deposited films and in chamber clean. Customized fluorine content allows etch selectivity with varying etch rates. These are used in silicon nitride and silicon oxide etch. For example, 1,3 hexafluorobutadiene (C4F6), hexafluoroethane (C2F6), methyl fluoride(CH3F), difluoromethane (CH2F2), trifluoromethane (CHF3), octafluorocyclobutane (C4F8), fluorine (F2), hydrogen fluoride (HF), hydrogen iodide (HI), hydrogen chloride (HCl) and others are used.
Rare gases: Mixtures of rare gases with others are used in lithography (EUV). In the semiconductor manufacturing industry, the photolithography process is used to create patterns on silicon wafers, an extremely important step in advanced devices. Mixtures of rare gases with other reactive chemistries are used. For example, neon, xenon and krypton. Rare gases are also used to modulate fluorocarbon etch chemistries during RIE to provide improved selectivity and etch rates in the latest technology nodes.
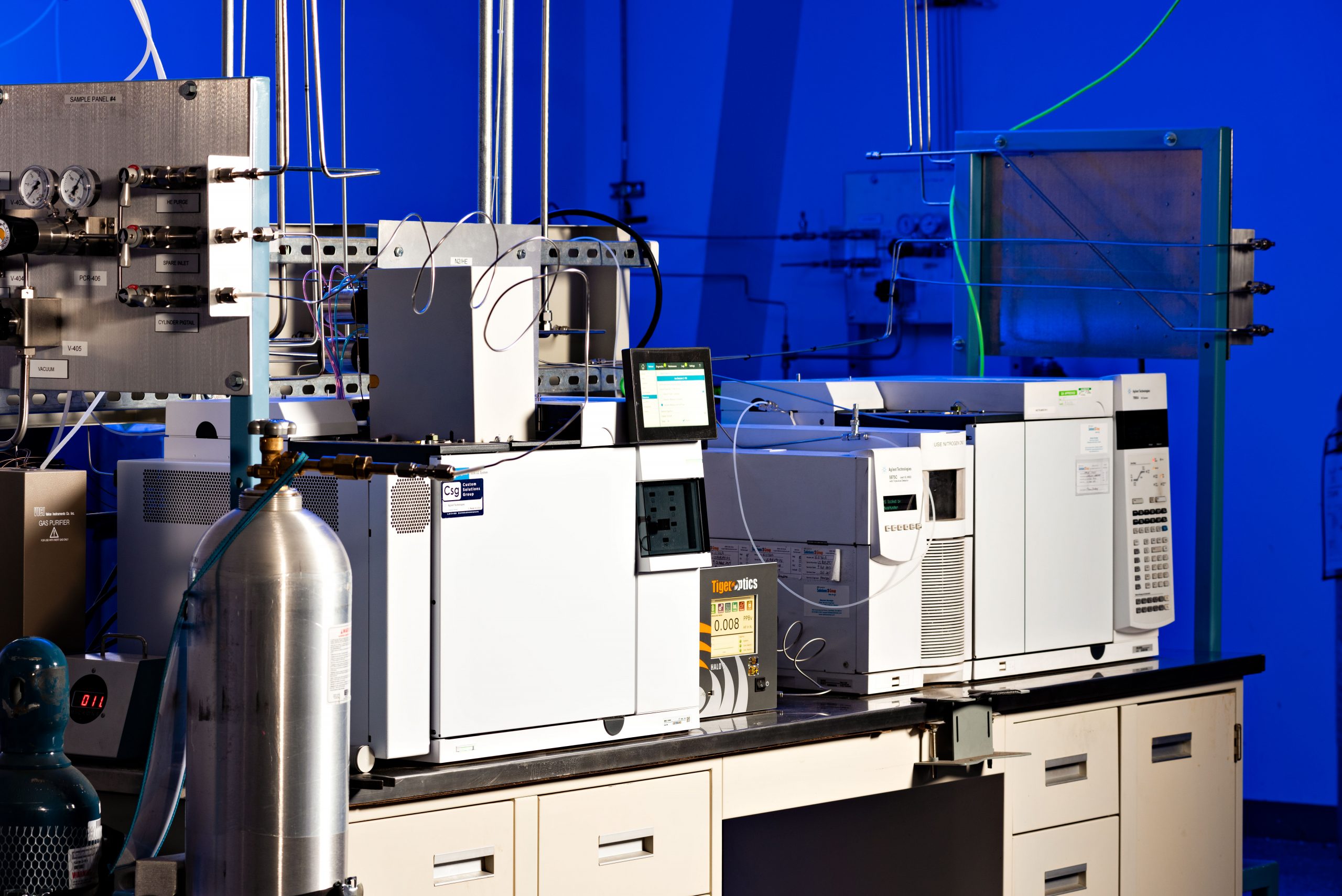
Our Commitment
Safety and environmental impact are an integral part of producing and handling of these semiconductor manufacturing gases. EFC Gases & Advanced Materials has developed industry leading software to track the use and recycling of high Global Warming Potential (GWP) molecules. As part of this software, EFC also offers recycling and traceability of critical molecules on EPA lists including the HFC Phasedown covering CHF3, CH2F2, and CH3F. Beyond tracing and recycling capabilities EFC is developing alternatives for etch processes for gases that rely upon high GWP gases such as CHF3 and SF6. To this end, EFC is committed to using stringent operating procedures when packaging these gases into meticulously prepared DOT approved cylinders. Cylinders are tracked using electronic bar code and EFC’s cylinder tracking system.
Electronic gases are not only used in microelectronics, but also in other fields of high technology, e.g., in the production of optical glass fibers, surface coating of materials and glasses as well as in the production of sensors and compound semiconductors such as solar cells.
EFC Gases & Advanced Materials’ production uses various adsorption, chemisorption, separation, and distillation techniques to transform low grade industrial materials into high-purity electronic gases in our own purification plants for optimum conformity to EFC’s customers’ requirements. EFC has a well-established management system for quality, safety, and the environment (QSE) in its operations and is certified by ISO 9001:2015 (quality management), internal safety management and will be ISO 14001 certified in the near future. EFC manages through rigorous quality management; our suppliers and service-providers. Customer complaints and deviations from our internal standards are systematically analyzed by standard 8D process for corrective and preventative measures.
Cylinder and package preparation is an integral part of our product portfolio. We offer a wide variety of packaging and special containers to ensure long shelf life and stability for our high purity hydrocarbon and fluorocarbon gases. Selection of the containers and cylinder valves are made based on chemical reactivity to ensure safety and process requirements. Cylinder materials used include hardened and tempered steels with inner surface treatment, passivated aluminum alloy or (electropolished) stainless steel. In all the cases cylinder valves are selected and employed after comprehensive testing. Both manual and pneumatic valves can be supplied. This will enable reliability of our products with low particle generation, leak tightness, effective purging for reliability and safe handling.
We have developed analytical processes with years of experience in fluorocarbon gas and specialty gas mixtures (reactive) with trace analysis of impurities in ultra-high purity gases for quality assurance. Many of these gases are also analyzed for trace metal impurities using ICPMS. Other leading-edge analytical methods such as applying novel gas chromatography calibration, detectors, methods and detector optimization, various forms of absorption and emission spectroscopy, combined with mass spectrometry are used to analyze a broad spectrum of impurities within our intermediate and finished product. Individual impurity specifications are reported on the certificate of analysis for every cylinder of gas. The data is collected and continuously analyzed for statistical quality control (SQC). The results of these analysis are available for evaluation and continuous improvements in our SPC for ongoing process. Quality, safety and environmental protection in the production, transportation and use of our products are an important part of our quality management systems and corporate philosophy.
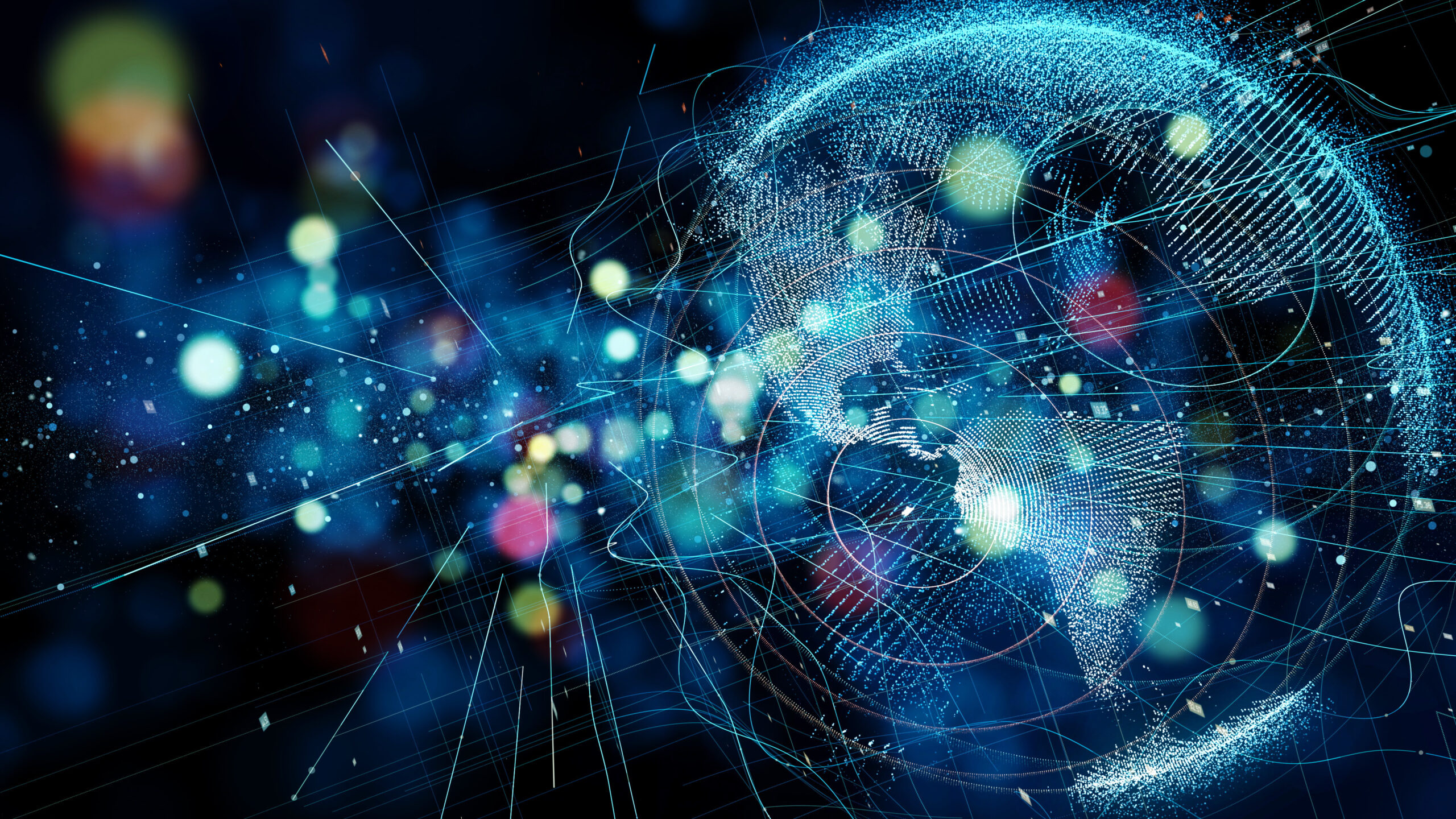
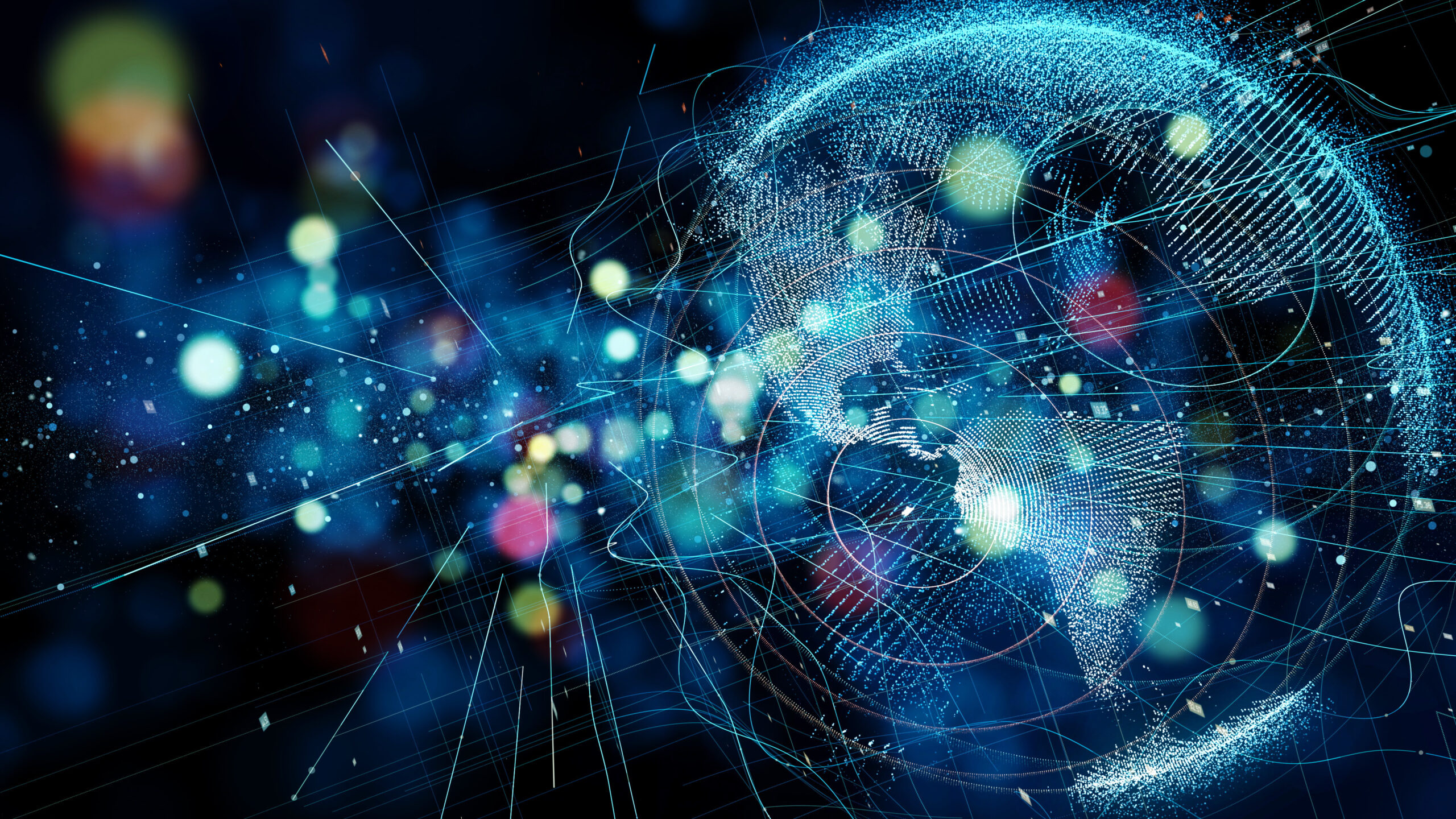
Related Content
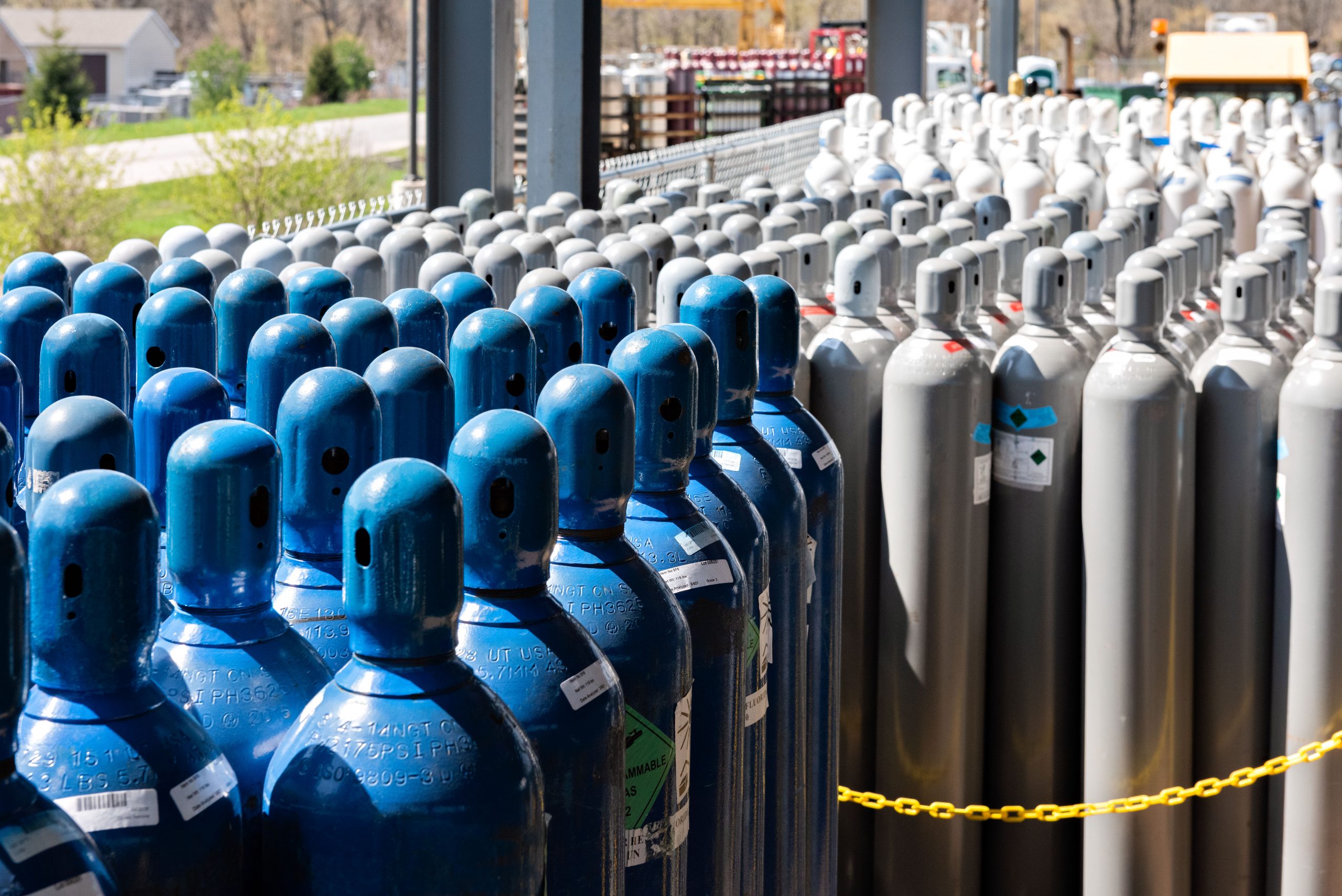
Our Gases
We have spent over 20 years evolving our strategy to meet the needs of our customers. We are service providers, working with you to overcome industry challenges. Looking for a specific gas? As your premier supplier of specialty gases, we have made it easy to shop by industry or by category.
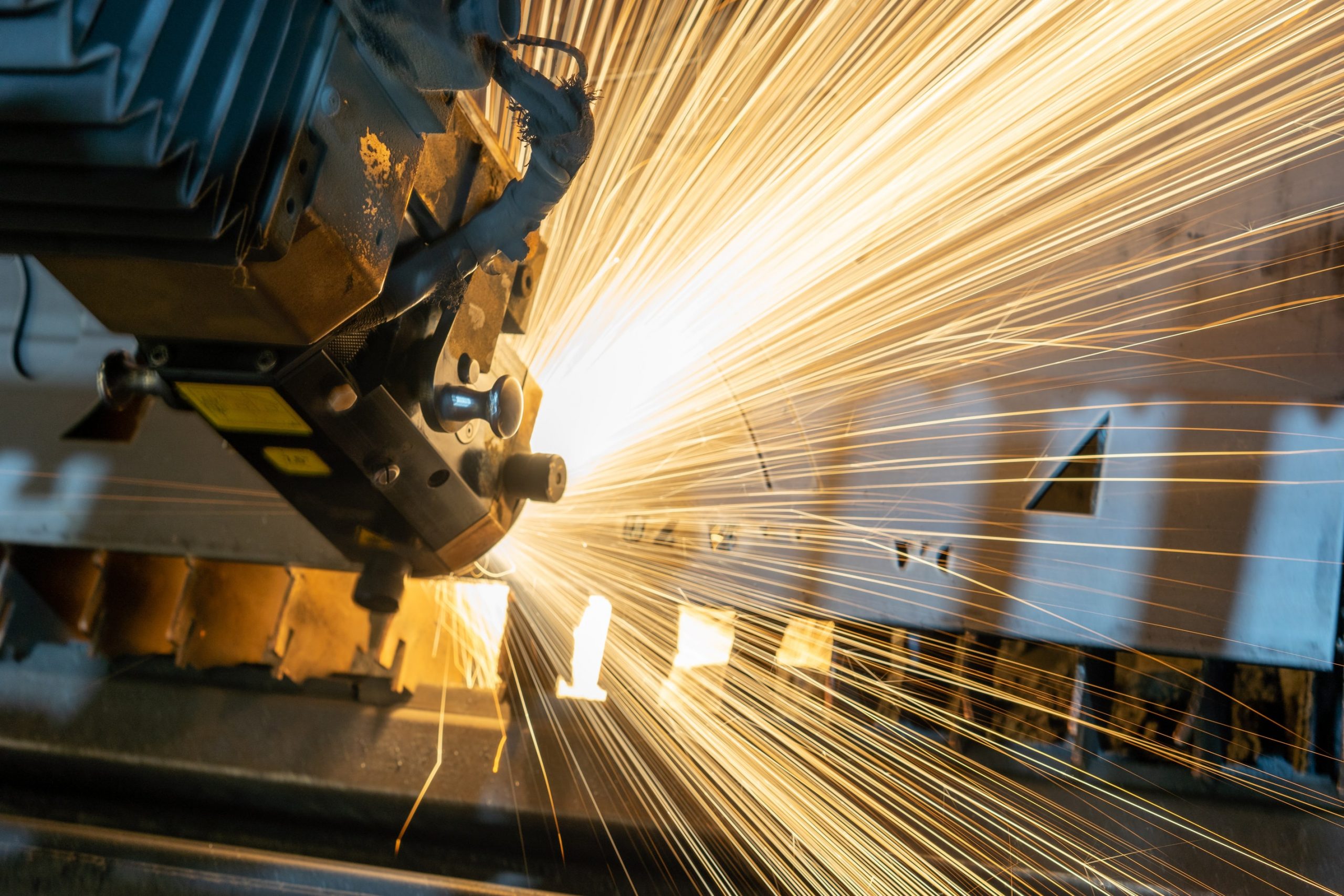
New R&D Building At Our Hatfield Plant
We are currently building a new Research & Development center at our Hatfield Plant. Scheduled to open this year, the product development area will be equipped with many advanced capabilities, including a pilot scale high-pressure high-temperature reactor and a specialized spinning band distillation system.
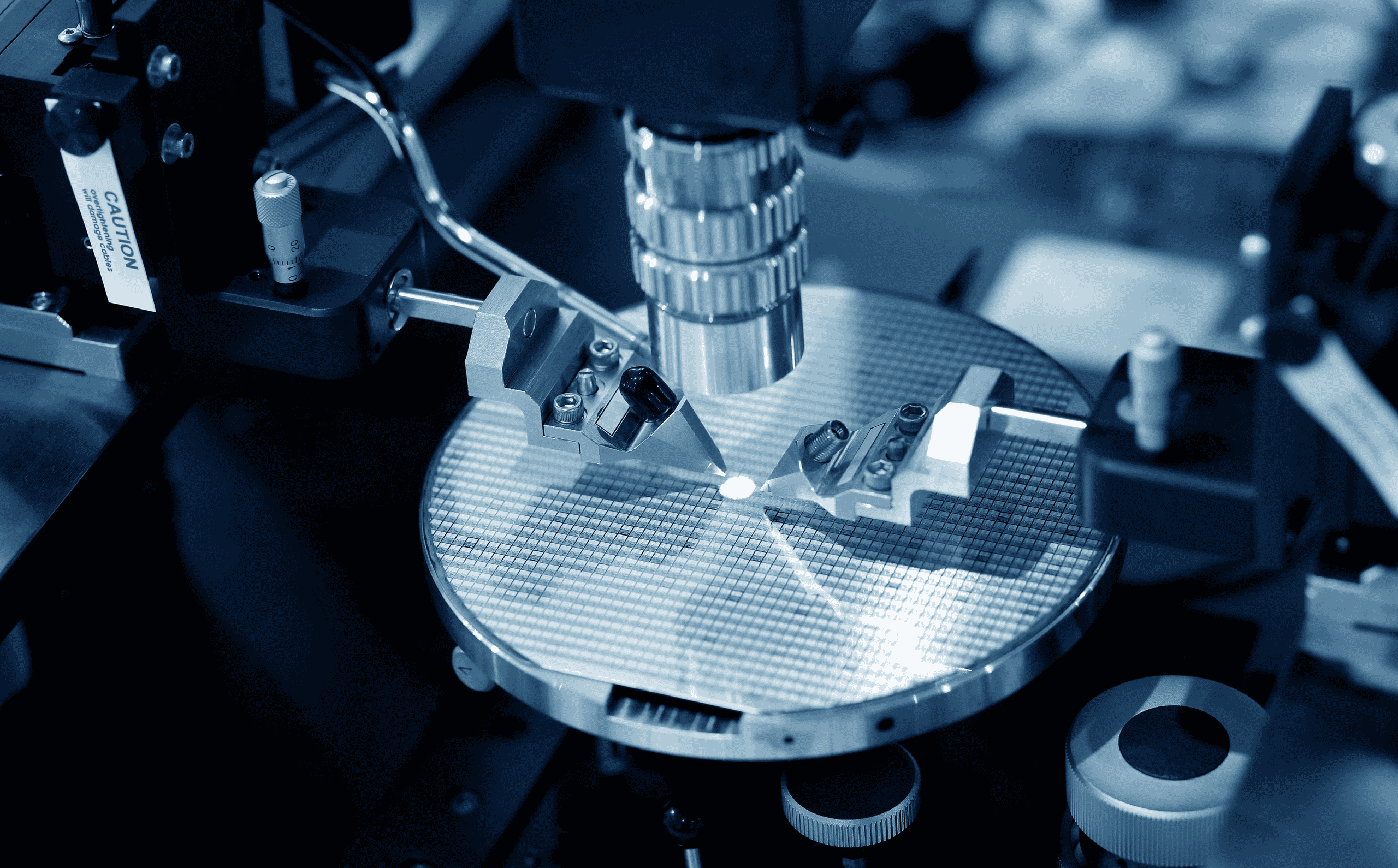
Semiconductors: Fabrication & high purity gases
We have historically provided to our customers our legacy products with the highest level of purity and quality coupled with state-of-the-art analytical characterization. As the technology nodes of semiconductor manufacturing continue to evolve, Electronic Fluorocarbons is investing now to establish advanced technologies for the synthesis, purification, and characterization of the electronic gases required today and in the future.