A preferred route to C4F6 involves the readily available raw materials ICl and CTFE in a 3-step synthetic process as illustrated below in Scheme 1. The basis of this chemistry has been known for nearly 70 years and was described in the past scientific literature by several workers including Hazeldine (J. Chem. Soc (1952) 4423), Hauptschein (JACS (1961) 83, 2495), and Ameduri (J. Fluorine Chem. (1995) 74, 261). Moreover, similar process chemistry is described in the Russian Patents, RU 2246477 and RU 2272017.
Step 1 involves the 1,2 addition of the interhalogen ICl to CTFE and results in formation of the major and a minor 1,2-addition products. In step 2, reductive coupling with zinc of
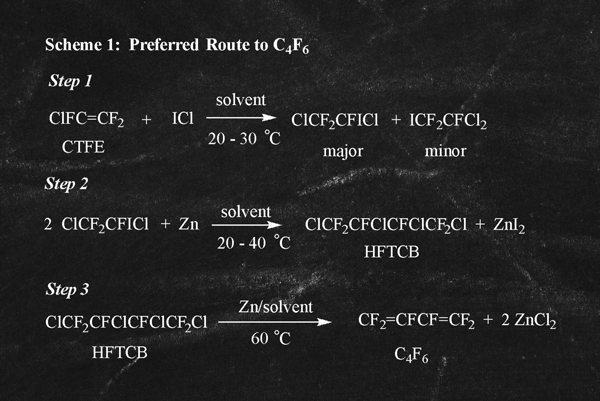
the 1,2-addition products provides the perhalogenated butane, HFTCB. In the third process step, HFTCB is reductively dechlorinated with zinc in a polar solvent to provide high purity C4F6. Purification of the final product often is facile owing to the large differences in volatility and polarity of C4F6 compared to the major contaminants such as organic solvent.
Finally, it is important to note that in this preferred ICl/CTFE route, the major by-products, ZnI2 and ZnCl2 , can readily be recovered and recycled through simple processing back to key raw materials as illustrated below in equations 1a to 1c:
The combination of ready availability of raw materials, simple chemical processing, and recyclability of all by-products makes this ICl/CTFE process a preferred route for industrial scale production of high purity C4F6.
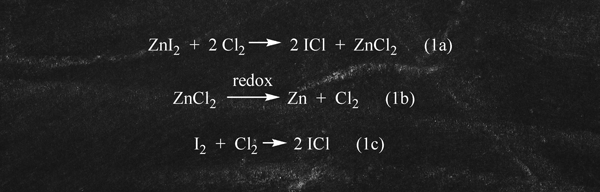
The combination of ready availability of raw materials, simple chemical processing, and recyclability of all by-products makes this ICl/CTFE process a preferred route for industrial scale production of high purity C4F6.
Alternative Route A: Thermal dimerization of (CTFE)
An alternative route to C4F6 involving pyrolysis of CTFE at 505-600 °C is described in a Russian Patent, RU 2,264,376 as well as in USP 2,668,182 (Examples 1-2) and is illustrated below in Scheme 2:
This process has a number of significant disadvantages when compared to the preferred ICl/CTFE route to C4F6.
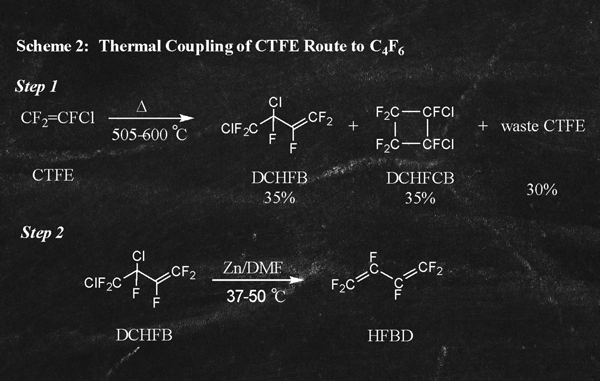
First, the initial pyrolysis of CTFE (Scheme 2, Step 1) leads to a mixture of 3 principal components: the desired 3,4-dichlorohexafluorobut-1-ene (DCHFB) at 35%; the by-product 1,2-dichloro hexafluorocyclobut-1-ene (DCHFCB) at 35%; and waste CTFE at 30%. After separation of the 3 principal components of the pyrolysis reaction it is only the 35% DCHFB that can be directly dehalogenated (RU 2,272,017) to provide C4F6 as illustrated above (Scheme 2, Step 2). Of the remaining by-products, DCHFCB (35%) cannot be directly recycled into the process and is often destroyed or simply stored. The waste CTFE portion (30%) in principle can be cleaned up and recycled, however, it often is disposed of such as in a thermal oxidizer system. The problem with destruction of waste CTFE is that it produces extremely toxic residues and other hazardous by-products of combustion that too must be subsequently treated as hazardous waste.
The greatest challenge remains, however, in dealing with the 35% DCHFCB that is produced in the initial pyrolysis reaction. This by-product has no downstream uses and cannot be efficiently disposed of through oxidation and combustion because of the highly toxic combustion products (COCl2 and COF2) that are formed. As a result, the only known method to deal with this significant volume of by-product is to store it indefinitely in a safe manner. This presents a number of significant problems including finding storage vessels of sufficient volume and chemical resistance to contain this waste stream for indefinite periods of storage. An unrelated yet analogous challenge can be found in the nuclear power generation industry where large volumes of depleted UF6 must be stored indefinitely and, unfortunately, are likely to create an environmental hazard at some point in the future.
Alternative Route B: Fluorination and Coupling of Trichloroethylene
A second alternative route to C4F6 involves multiple process steps starting with trichloroethylene (HCO-1120) and elemental F2 as described in USP 8,536,387 and as illustrated in Scheme 3a (right).
There are numerous process disadvantages to this route starting with trichloroethylene and as described in USP 8,536,387 (Examples 1-4). First, in Scheme 3a, Step 1, elemental F2 is employed to provide a fluorinated and coupled product DFHCB. These radical coupling steps are inherently challenging and often times occur with low conversion and overall yield. Following this low-yielding coupling step, DFHCB is dehydrochlorinated (Scheme 3a, Step 2) and subsequently fluorinated (Scheme 3a, Step 3) with elemental F2 to provide the desired HFTCB. In the fourth and final step (Scheme 3a, Step 4), HFTCB is dechlorinated to provide the desired C4F6 product.
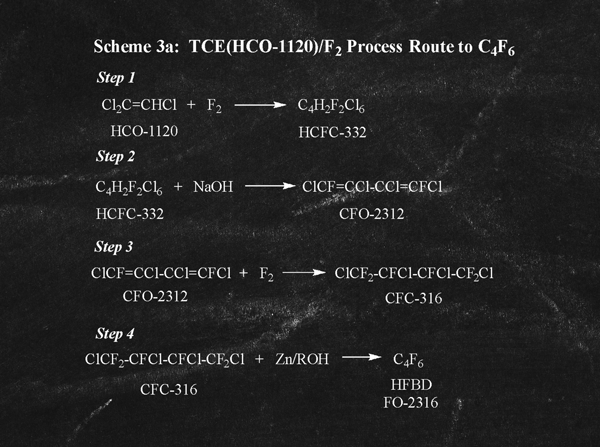
The combination of poor conversions and cumulative yields throughout four processing steps (cumulative yield as documented in Examples 1-4 is 33.5%) makes this an undesirable process option for industrial scale production of C4F6.
Note that USP 8,536,387 also teaches (in Examples 6-9) that the fluorination and coupling process steps illustrated in Scheme 3 can be reversed as depicted in Scheme 3b (left).
In the case of Scheme 3b, the cumulative process yield as described in USP 8,536,387 is about 12%. Thus, the combination of poor yield and the need to employ elemental F2 on an industrial scale makes this process to C4F6 highly undesirable.
Alternative Route C: Chlorination/Fluorination of Butadiene
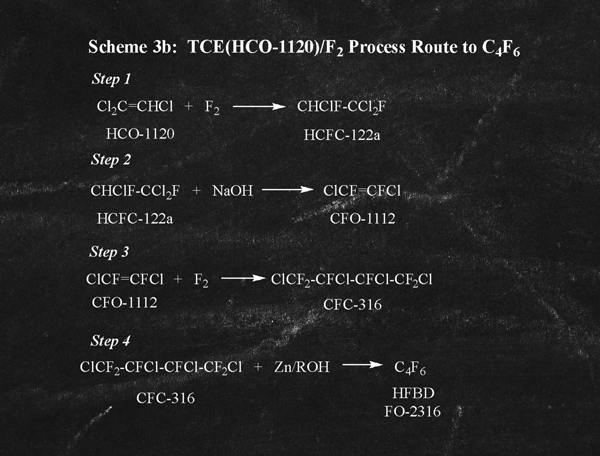
A third alternative route to C4F6 involves formation of the key intermediate (CFC-316) by fluorination of a reaction by-product of the chloroprene rubber industry and is described in USP 8,030,528 and illustrated in Scheme 4 (right).
Step 1 of Scheme 4 illustrates the first step in the industrial scale production of chloroprene rubber. Chlorination of 1,3-butadiene leads to a mixture of products including HCO-1370 that is further processed in the production of chloroprene rubber and CHC-370 which must be separated and either further processed, or disposed of as a waste product. In Step 2, HCO-1370 can be further chlorinated to generate the key intermediate CHC-370. In Step 3, direct fluorination leads to the key intermediate to C4F6, CFC-316 which subsequently can be reductively dechlorinated to C4F6 using zinc as shown in Step 4.
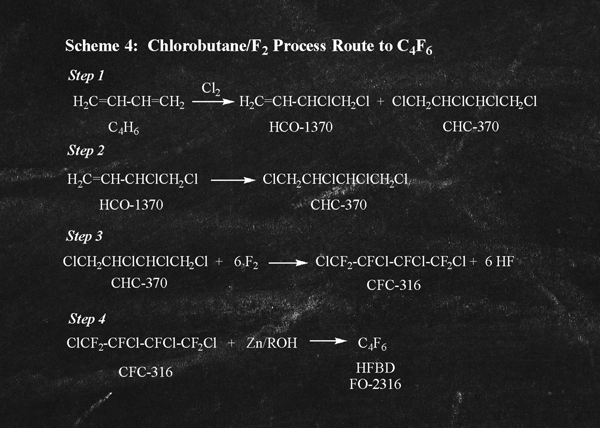
There are a number of process disadvantages to using this route for the primary production of C4F6. First, the key intermediate (CHC-370) occurs only as a minor by-product in the chloroprene rubber production process. Thus, if the chloroprene rubber industry experiences a slowdown, the production of CHC-370 will similarly be reduced. Secondly, chlorination of HCO-1370 is problematic with formation of over chlorinated by-products (heavies) that must be separated and disposed of (incinerated). Thirdly, the fluorination Step 3 requires 6 equivalents of F2 per equivalent of CHC-370 and produces 6 equivalents of by-product HF that must either be disposed of (neutralization) or with great difficulty, separated, purified, and recycled to a F2 generator. In other words, only 50% of the fluorine atoms introduced in Step 3 are actually used in the production of CFC-316.
In light of the high dependence on the chloroprene production industry and the multiple waste generating chlorination and fluorination steps, this chlorobutane/F2 route (Alternative route C) to C4F6 is inferior to the preferred process described heretofore in Route 1.
Alternative Route D: Miscellaneous Non-industrial routes to C4F6
There are a number of alternative non-industrial routes known for the formation of C4F6. These alternative routes are not practical for use as industrial processes owing to a number of factors including the complexity of the chemistry and unavailability of key raw materials. For illustration purposes, just two of these alternative routes are discussed hereafter. In the PCT Application WO2006/026400 and in the Journal of Fluorine Chemistry (Vol 129, pp 443-446, 2008) Ramachandran et. al. describes a route to C4F6 involving coupling of bromotrifluoroethylene (Scheme 5)
There are a number of alternative non-industrial routes known for the formation of C4F6. These alternative routes are not practical for use as industrial processes owing to a number of factors including the complexity of the chemistry and unavailability of key raw materials. For illustration purposes, just two of these alternative routes are discussed hereafter. In the PCT Application WO2006/026400 and in the Journal of Fluorine Chemistry (Vol 129, pp 443-446, 2008) Ramachandran et. al. describes a route to C4F6 involving coupling of bromotrifluoroethylene (Scheme 5)
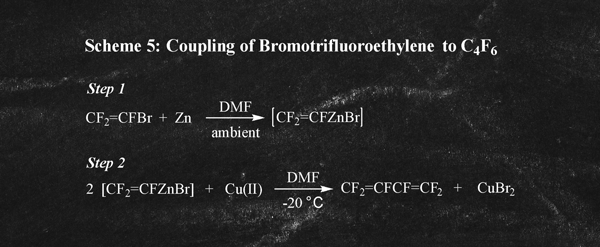
Bromotrifluoroethylene is a highly restricted ozone depleting substance that is not produced commercially. Another route to C4F6 described by the same authors involves derivatization and coupling of HFC-134a as illustrated in Scheme 6. There are obvious disadvantages of both process routes especially for industrial scale production of C4F6. As a result, neither route to C4F6 is commercially viable and they have only been practiced on a laboratory scale.
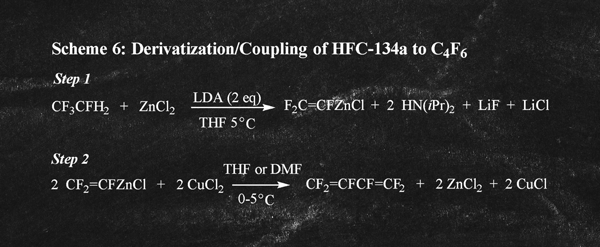
Summary
A preferred synthetic route involving ICl and CTFE and a number of alternative routes employing a range of different starting materials and process operations have been described for the industrial scale production of hexafluoro-1,3-butadiene (HFBD), C4F6.